عربي | Careers | Contact Us | Downloads

Rapidwall Plant
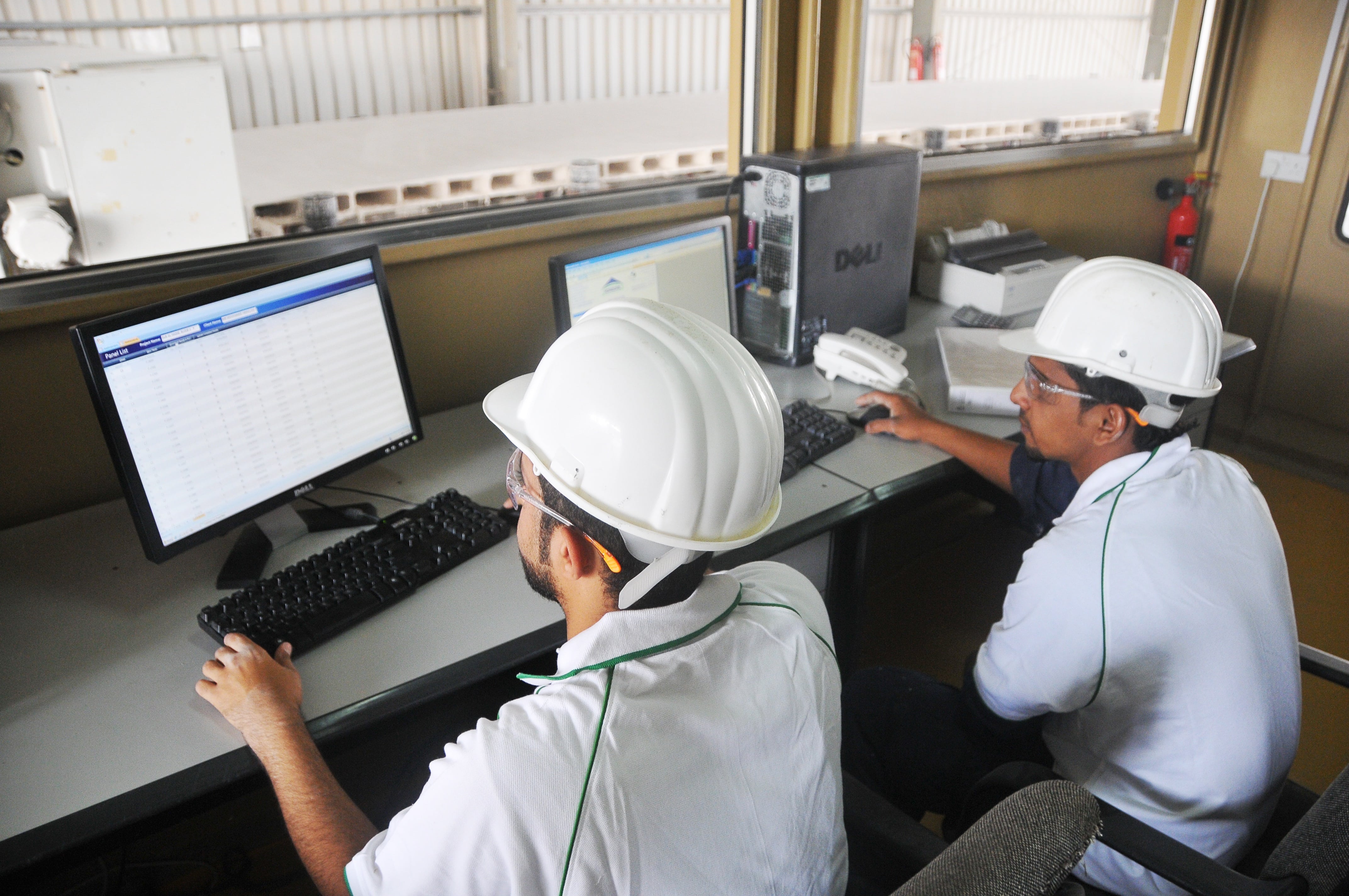
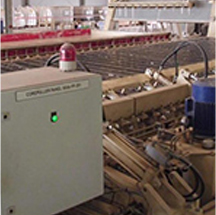
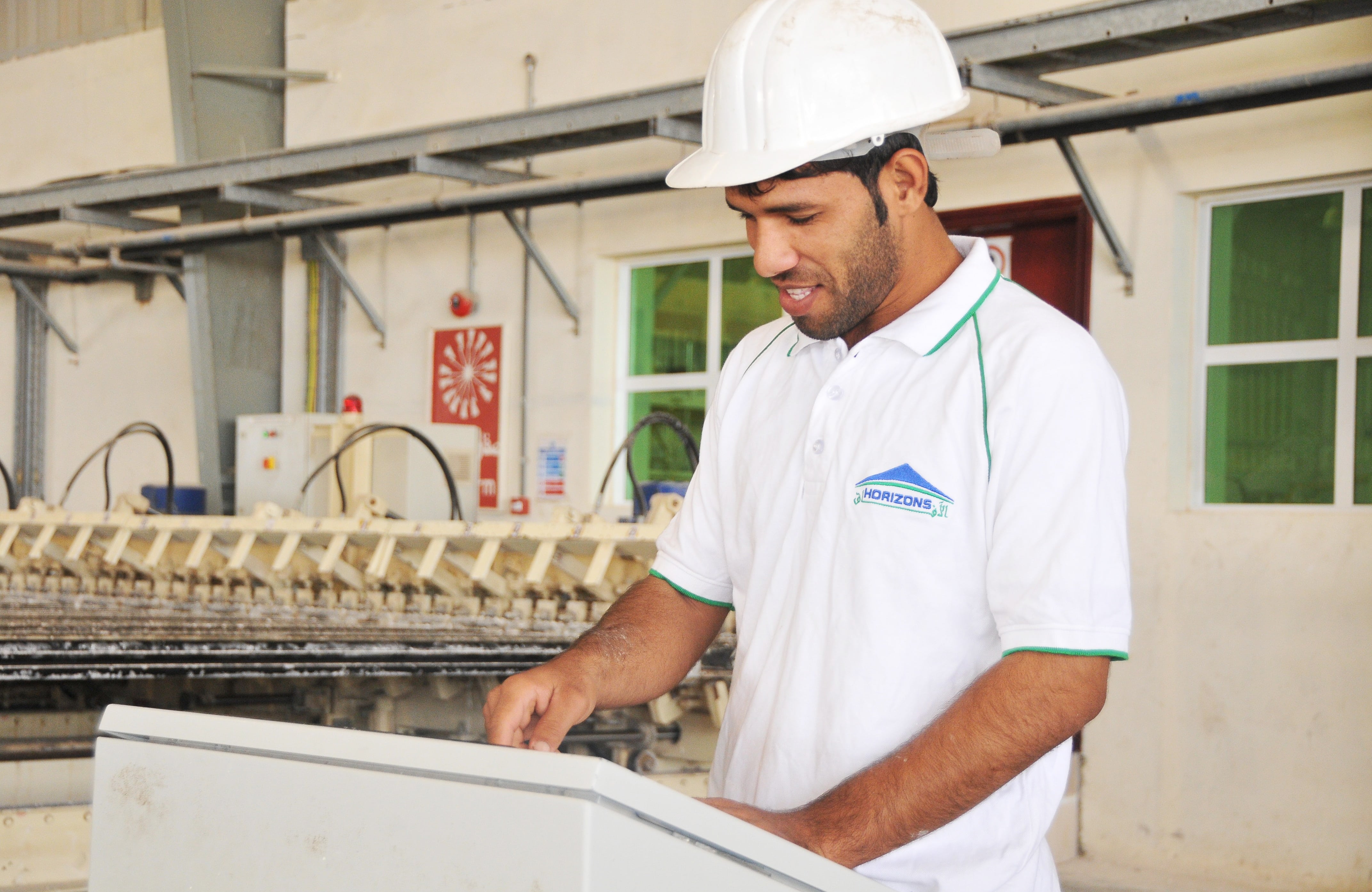
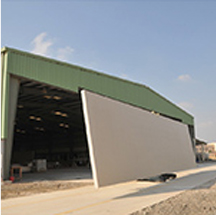
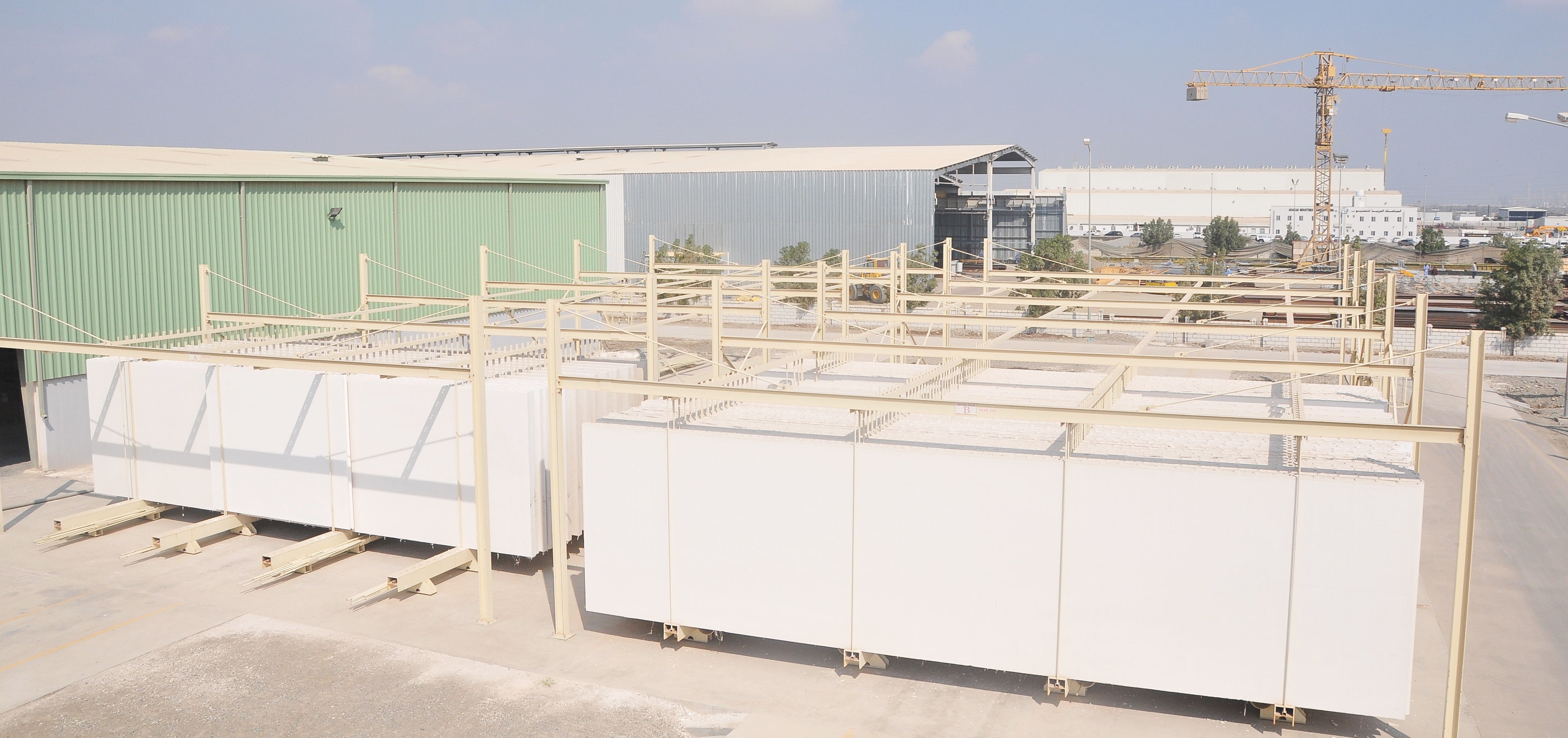
The Product
Rapidwall is a precast gypsum based walling panel produced by the company Horizons industrial development company. Rapidwall is manufactured off site in a Rapidwall production unit. The Rapidwall production factory is located on Sohar Industrial Area Phase III, Sohar, Sultanate of Oman.
The Rapidwall System streamlines the construction process by transferring the majority of on-site work to the Rapidwall factory. It is within the factory that the large single spanning walls, roofs and ceilings are produced. These building components are then easily erected on site in a matter of hours rather than weeks.
Rapidwall panels are lightweight modular building panels produced by moulding fiberglass reinforced gypsum. The lightweight of the panels is created through the use of plaster and the void space (void chambers) in between the two skins.
A basic panel is manufactured commonly in the size 12 x 3 m (36 m2) on a casting table, which is the production unit for Rapidwall, and in a large enough size to form an entire wall of a building structure. It is cut easily either at the factory or site and can be tailored to a great variety of designs, including window and door requirements.
Gypsum is naturally occurring, abundant resources are available worldwide. Both natural gypsum as well as by-product or waste gypsum can be used as the raw material for the plaster production.
HIDC have been operating, testing and perfecting Sohar plant for the manufacture of Rapidwalls since 2009. One Rapid Building Systems plant with three manufacturing tables would produce approximately 700,000 m2 of panel per annum, 2,462 m2 a day, based on a 24 hour production schedule over 300 days. This equates to more than 2000houses of 120 m2 each including roofs.
Drying Methods
Once a panel is removed from the table it is still too wet to be further processed. Panels gain their full product strength when they reach certain dryness.
Horizons use air-drying method. Within this method panels are lifted onto storage racks where drying takes between 5 and two weeks, depending on the outside temperature. The main advantage is that no energy is consumed for air-drying. The disadvantages are that the drying time is relatively long and a huge stock of panels on the premise is created.
Cutting of Rapidwall and Preparing for Dispatch
The Cutting Area is located directly next to the drying room. Cutting is essential in the manufacturing process of Rapidwall. A dried panel is ready for the construction of a building, but in most cases has to be cut to size to match design applications of architects. Once drying is finished Rapidwall can be tailored to a great variety of designs. Most common are vertical or horizontal cuts by a circular saw on basic panels. Panels are cut to a smaller size or door and window cut-outs are performed.
A Rebate is a connection between two panels on a wall, which are set up on site on and it is precut from factory
The factory manager organizes the whole cutting process. The first step is that a hardcopy of drawings of a building is send to horizons by the Customer or Architect. In addition, the cutting schedule is send via E- mail. The factory manager creates a Stillage Packing List from this information. A stillage is a metal frame, which is used to dispatch Rapidwall. Creating a packing list is a logistical task, where on one hand the transport truck has to be loaded as good as possible and on the other hand panels have to be packed in the right order so that setting up on site can be done easier. Once a packing list is created a draft is send to the customer for approval. If the draft is approved, the cutting schedule and the drawings are transferred to the cutting area. Here cutting, studding and stillaging of Rapidwall are done in accordance to the packing list, cutting schedule and the drawings.
The cutting area is equipped with a programmable computerized circular saw. Several cutting commands for one panel can be programmed at the same time on a touch screen terminal, The basic panel sits on a rack and the saw is moved on a track along the panel.